A Comprehensive Checklist for Effective Welding Evaluation Practices
In the world of welding, the stability of structures is paramount, demanding an extensive method to evaluation practices. A detailed checklist works as a crucial device in guaranteeing adherence to market criteria, incorporating essential pre-welding, in-process, and post-welding evaluations. By methodically addressing material confirmation, weld top quality, and extensive paperwork, organizations can significantly improve safety and security and efficiency. What specific elements should be prioritized in each phase to accomplish optimum outcomes? Exploring these essential elements can produce understandings that exceptionally effect welding operations.
Comprehending Welding Standards
Welding requirements play a crucial function in ensuring the high quality and safety of bonded components and structures. These requirements establish the standards for products, procedures, screening, and inspection, therefore supplying a structure for constant quality control in welding procedures. Numerous organizations, including the American Welding Culture (AWS), the International Organization for Standardization (ISO), and the American Society of Mechanical Engineers (ASME), have created detailed requirements that govern various facets of welding.
Recognizing welding requirements is important for experts in the field, as adherence to these guidelines decreases the danger of issues and failures in welded joints. These requirements cover specific demands for weld top quality, including acceptable tolerances, the kind of welding techniques to be made use of, and the credentials needed for assessors and welders.
Pre-Welding Evaluation Steps
Prior to any welding process commences, a complete pre-welding evaluation is vital to recognize prospective issues that might endanger the top quality of the weld. This preliminary action works as a crucial structure for making certain compliance with suitable welding codes and criteria.
The very first step in the pre-welding assessment is to validate the products being utilized. This consists of checking for the right kind and grade of steels as specified in the task documents. Next off, it is crucial to inspect the fit-up of the elements to make certain correct positioning and joint configuration. Imbalance can bring about inadequate infiltration and architectural weak points.
In addition, reviewing the sanitation of the surface areas is crucial; contaminants such as oil, rust, or paint can negatively impact the top quality of the weld. Following this, a detailed assessment of the welding tools need to be conducted, ensuring that it is calibrated and in good working problem.
Last but not least, assessing the certifications of the welding workers is vital. Welders have to have the necessary qualifications and experience to carry out the specific welds needed for the job. By adhering to these pre-welding examination steps, the likelihood of flaws and failures in the final weld can be dramatically minimized.

In-Process Examination Techniques
In-process evaluation strategies play an essential duty in making sure the integrity and high quality of welds as they are being carried out. These techniques permit inspectors to recognize problems or inconsistencies from requirements in actual time, therefore guaranteeing and avoiding expensive repair services adherence to design needs.
One trick strategy entails aesthetic evaluation, where assessors analyze the weld bead for harmony, penetration, and proper profile. This can be matched by the use gauges to gauge weld measurements, making certain compliance with predetermined resistances. Additionally, the implementation of non-destructive testing (NDT) approaches, such as ultrasonic testing or magnetic bit testing, throughout the welding procedure can reveal subsurface defects that might not show up on the surface.
An additional vital aspect is keeping an eye on welding parameters, including voltage, amperage, and travel speed. Uniformity in these specifications is critical for accomplishing ideal weld quality. Documenting these parameters during the welding procedure gives a deducible record for future recommendation.
Training personnel in appropriate examination techniques and making read review use of ideal devices enhances the performance of in-process examinations. By integrating these techniques, organizations can achieve greater high quality welds, lower rework, and ultimately ensure the safety and security and dependability of welded frameworks.
Post-Welding Top Quality Checks
Following the conclusion of welding operations, post-welding top quality checks are critical to validate that the welds fulfill all defined standards and demands. These checks are necessary for making certain the honesty and toughness of the welded joints. The examination process commonly starts with an aesthetic assessment, analyzing for surface flaws such as splits, porosity, or incomplete fusion.
Consequently, non-destructive screening (NDT) techniques, such as ultrasonic screening, radiographic screening, or magnetic bit testing, might be used to detect internal flaws that are not Going Here visible to the nude eye. Each method has its distinct advantages and is picked based upon the weld's location, material kind, and the nature of the application.
Additionally, confirming dimensional accuracy is an important aspect of post-welding top quality checks. This includes measuring the weld's placement, account, and size to guarantee compliance with engineering requirements. Lastly, analyzing the mechanical buildings of the weld, consisting of tensile toughness and ductility, can provide additional assurance of efficiency under operational conditions. In general, complete post-welding inspections are essential for keeping efficiency, security, and adherence to governing and market criteria.
Paperwork and Reporting
Just how can effective paperwork and reporting boost the welding inspection procedure? Precise documentation and comprehensive reporting are essential elements that ensure the honesty and top quality of welding operations. Welding Inspection Milwaukee. They serve as an official document of assessment findings, helping with liability and traceability in conformity with market standards

A well-structured reporting system enables inspectors to plainly connect any kind of areas, discrepancies, or non-conformances calling for improvement. This openness fosters a setting of continuous enhancement, as stakeholders can easily analyze past efficiency and carry out restorative actions.
Moreover, effective documents consists of comprehensive records such as welding procedure specifications (WPS), welder certifications, and assessment lists. These aspects supply a structure for assessing weld quality and adherence to established standards. In case of disputes or top quality concerns, complete documents acts web as a trusted reference, decreasing ambiguity and shielding all parties involved.
Last but not least, maintaining organized documents aids in training and accrediting personnel, making sure that sector best methods are maintained. Eventually, thorough paperwork and reporting not just boost the welding inspection procedure yet additionally contribute to the overall security and dependability of bonded frameworks.
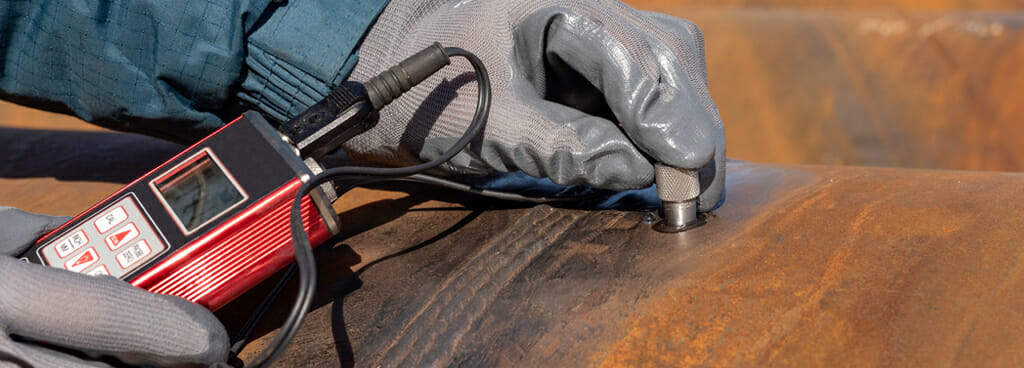
Conclusion
In final thought, a detailed checklist for efficient welding inspection techniques is important for ensuring top quality and safety in welded structures. Adherence to established welding requirements, careful pre-welding evaluations, rigorous in-process analyses, and thorough post-welding top quality checks jointly contribute to the integrity of welded joints.
Welding criteria play an important duty in ensuring the high quality and security of bonded parts and frameworks. Different organizations, including the American Welding Society (AWS), the International Organization for Standardization (ISO), and the American Culture of Mechanical Engineers (ASME), have actually created detailed standards that govern various facets of welding.
Following the conclusion of welding operations, post-welding quality checks are critical to validate that the welds fulfill all specified standards and needs - Welding Inspection Milwaukee.In final thought, a detailed list for efficient welding inspection techniques is essential for making sure high quality and security in bonded structures. Adherence to established welding standards, thorough pre-welding inspections, strenuous in-process assessments, and thorough post-welding quality checks jointly add to the honesty of welded joints